Sunday, with my indoor housework completed, I’d run out of excuses not to install Glinda’s recently rebuilt original distributor. With Ringo still parked in the garage, I had to deal with single-digit wind chills. So I bundled up and got her done. The job
should have been fairly straightforward and completed in about an hour, but a screw-up turned it into a two hour affair.
Can you spot the difference between my assembly on the left and a proper assembly on the right?
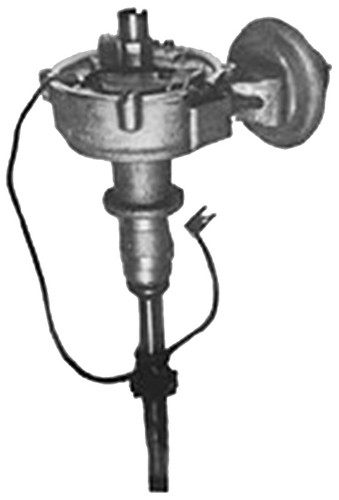
Here’s a hint. After installing the rebuilt distributor and cranking the engine to check the dwell, the distributor shaft was not turning with the engine.
That’s right; the drive gear was installed upside down. What a moronic maneuver on my part. Instead of verifying the orientation with one of many references I have, I looked at the shaft and assumed the orientation based on the marks on the shaft. Oh well, live and learn – AGAIN.
It only took me about twenty minutes to remove the distributor from the engine, press the pin back out, reverse the gear, and reinsert the pin. Next came the harder part. Since the engine had turned, I now had no idea where the rotor needed to be pointing. Using a wrench, I rotated the crank until the timing mark sat at top dead center (TDC). Know it was a fifty-fifty chance I was out 180 degrees, I installed the distributor with the rotor pointing at the number one plug contact in the cap. In order to get the shaft fully seated, I needed to crank the engine slowly with a wrench until the rib in the end of the shaft fell into the slot of the oil pump. Next, I needed to set the dwell by cranking the engine and adjusting the point gap until the meter read around 32 degrees. With my fingers crossed and the rotor, cap, and wires in place, I cranked the engine. Of course my bad luck held out and the engine wouldn’t start, so I had to re-remove the clamping hardware, pull the distributor out again, rotate the shaft a half a turn, drop it back in place, and re-reinstall the clamp, retainer, and nut. After that the engine fired right up. Thank the good Lord for small miracles. I checked the dwell and it was rock-solid at 34 degrees; right at the spec’s. limit. After letting the engine warm up enough to get the carbs off high-idle, I set the timing to the highest mark on the engine case - 16 degrees BTDC. This is above the 12 degrees the manual states, but I decided to push it based on the cold temperatures and 93 octane gas we’ve been putting in Glinda’s tank. I knew I’d be driving her the next day on the interstate and if the engine pinged, I’d back down the timing accordingly.
Within 36 hours of this task, I’ve driven her exclusively, putting around 60 miles of mixed driving including 70+ mph romps on I-70 up hills. No pinging! And when I filled the gas tank yesterday afternoon, the mileage was over 17 mpg from the 15 she’d been previously getting. Bearing in mind, half the tank had been burned before the distributor and timing change, I expect even better gas mileage in the future. When the weather warms up again, I'll see if I need to retard the timing some. It also appears putting the stock distributor back in has mostly fixed the bogging at 65 mph. It’s still there, but not nearly as bad as before.