Friday, September 30, 2011
Still Fillin’
Had a bit of a date night with the lovely Loriann, so I limited my time in the garage. I did, however, get Wednesday evening’s body filler sanded down. I took a slightly different approach on the areas in front of the rear wheelwells. These surfaces are made up of compound curves, so rather than using my straight sander, I’ve been working the area by hand. I’ve not been happy with the undulations that still exist, so I cut some PVC pipe sections of different diameters, wrapped them in sandpaper, and used them to work the areas. I got much better results, but it did show that more filler was needed, so that went on in those two areas before I shut out the lights. I feel like I’m very close to the end of bodywork. Tomorrow, I should be able to roll Ringo into the sunshine and scuff the rest of his black paint in preparation for priming.
Thursday, September 29, 2011
One Coat Down, One(?) More To Go
Well, I’m cautiously optimistic that last night’s application of Everglass body filler is Ringo’s last. I first sanded down the previous night’s coat noting that only four areas still needed some filling. Once the one batch of filler was mixed and applied, I moved on to other projects.
The first of which was the shifting issue. With Ringo’s rear end up on jackstands and mine on a piece of cardboard on the floor, I drained the transmission fluid and dropped the Powerglide’s pan. With the bottom-side guts exposed, it was easy to get the small ball on the end of the shifter cable properly inserted into its nifty little cage. Sadly, while pulling the cable back to do the reinsertion, the other end popped off the dash-mounted shifter sending the tiny e-clip off into oblivion. I tried for a few minutes to find it by dragging a magnet all across Ringo’s floor, but my only catch was grinding dust. Irr. Add another part to the list. After cleaning off the mounting flange of the pan, I used the last of the tube of RTV to put a fine coat of blue mush across the mating face. The air-wrench spun the dozen or so bolts back into place and a crescent wrench torqued down the dipstick tube retainer. Now I can safely run the engine without worrying about Ringo trying to take off down the driveway.
The second issue I addressed was the stretched parking brake cables. Fifty years of being pulled to lock the rear brakes has probably added a few inches to the overall length of these two cables. Rather than spend the $100 on new ones while these are still structurally sound, I decided to utilize a cable shortener I’d pulled off of one of the Corvairs I’ve parted out. I backed off the tensioning nut on the front-to-back cable and installed the shortener using all its shortening capability. I’ll make the final adjustment to the tensioning nut after Ringo’s on ramps since the dangling rear wheels have an effect on the length of the side-to-side cable.
The first of which was the shifting issue. With Ringo’s rear end up on jackstands and mine on a piece of cardboard on the floor, I drained the transmission fluid and dropped the Powerglide’s pan. With the bottom-side guts exposed, it was easy to get the small ball on the end of the shifter cable properly inserted into its nifty little cage. Sadly, while pulling the cable back to do the reinsertion, the other end popped off the dash-mounted shifter sending the tiny e-clip off into oblivion. I tried for a few minutes to find it by dragging a magnet all across Ringo’s floor, but my only catch was grinding dust. Irr. Add another part to the list. After cleaning off the mounting flange of the pan, I used the last of the tube of RTV to put a fine coat of blue mush across the mating face. The air-wrench spun the dozen or so bolts back into place and a crescent wrench torqued down the dipstick tube retainer. Now I can safely run the engine without worrying about Ringo trying to take off down the driveway.
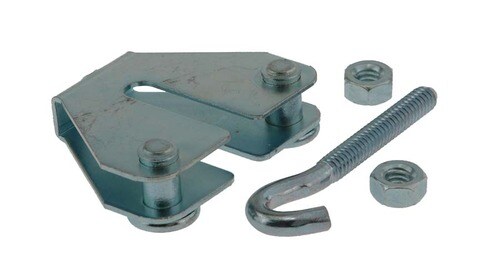
Wednesday, September 28, 2011
Running out of Bondo Opportunities

Most of last evening was spent making dust from bodyfiller. I hit all the spots that I’d laid down the other night and found that I’m optimistically still looking at one more layer (realistically, two – really realistically, three). Each time, however, the number of spots that need more filler is reduced. One new thing I did last night was get out my profile sander and put back the grooves in the front valence I’d, for the most part, filled in when patching rust holes. It’s not perfect, but there’s consistency again.
With the sanding done, I wiped down the areas still needing more Everglass and mixed and applied a couple batches. Tonight I’ll sand them down and see where that leaves me.
After I was done doing the filler, I still had about a half-hour left of garage time, so I used it to clean the backlight of sealer. Now it’s ready for reinstallation once the paint job is complete.
Monday, September 26, 2011
It’s Alive
Saturday I finished sanding the body filler on Ringo and then rolled it out of the garage and under the cloudy skies. With all the dust blown off, I wiped down the areas that needed more filler and then mixed and applied about a half-dozen golfball size batches of Everglass.





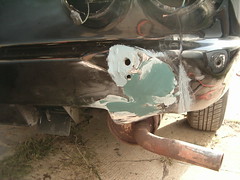
After a walk with the lovely Loriann to buy motor oil at Advance Auto, I filled Ringo’s engine crankcase and added an ounce of ZDDP additive. Then, with my electric drill and a 3/8 diameter bar with a flat milled in one end, I primed the oil system by spinning the pump input at the bottom of the distributor bore for a few seconds noting the Temp/Press light went dark soon after starting. That is a good thing. I also noticed an increase in torque required to turn the pump once the light went off. Also good. I then rotated the engine some and repeated the priming. After going all the way around the engine twice, I pronounced the engine fully primed, pushed it back into the garage, and called it a day.
Yesterday, after lunch, Mikhaila and I took a trip to Sears where I bought a DieHard to replace Ringo’s dead battery.
I was now ready for the rebuilt engine’s initial startup. I rolled Ringo back into driveway and installed the distributor being careful to get the rotor pointing at the #1 terminal on the cap with the timing mark at 8 deg BTDC. To static set the timing a little more accurately, I hooked up my timing light and turned the distributor counter-clockwise until the light flashed. With the clamp secured, I then connected the battery, hooked up the carburetor linkage, turned the key to on, hooked up a jumper wire to energize the solenoid, slipped one end of a hose over the fuel line inlet and immersed the other in a can of gas, poured some gas down each carb, and touched the jumper wire to positive. A big click from the solenoid, but and nothing else. Crap, bad starter. When assembling this engine, I chose the best-looking GUPs, and this starter had the cleanest solenoid. Guess I should’ve tested it. Half an hour later the starter was lying on the garage floor. I discovered the solenoid’s main connector was missing one of its nuts, so it was loose. With the battery hooked directly to the starter, it now tested fine. In the meantime I’d also pulled another GUP starter off the shelf and it also tested fine. I decided to install that one and hold the previous one in reserve. Another thirty minutes of assembly, and everything was ready to go again. This time touching the jumper to positive resulted in a spinning engine, but, sadly, nothing more other than some backfiring from the right carb. I poured a little more gas down each carb and tried again. Nothing different. Not liking what I saw in the right carb, I swapped it with another one that had tested out okay the other day. No difference. Since it appeared the fuel pump wasn’t priming, I pulled the tops off the two carbs and filled the now-dry bowls. More cranking and still no running and still some popping from the right side. Concerned I had a valve adjustment issue on the right side, I pulled those three plugs and tested compression. All three, thankfully, pumped up to 120 psi. I put the plugs back in and checked dwell. I’d set the points at .016, but with the engine only turning by the starter, the dwellmeter was only showing 20 degrees where I wanted 32. I tweaked the gap until the dwell was a little over 30 degrees. I static timed the distributor again and energized the solenoid. The engine still didn’t want to run. I then decided to put the timing light on and verify my static timing. With the starter turning the engine, I couldn’t see the timing mark when the light flashed. Irr. Not sure why the static timing method was so far off, I twisted the distributor first one direction and then the other. Finally, with it turned to about 20 degrees more advanced than my static setting, the engine started running. It didn’t run for long since it was back to using what little gas I poured down the venturis. It was now dinner time, so I kept the battery on the charger, and headed inside for break. After dinner, I rigged up a fuel supply system that gravity fed the carbs though a long fuel line with a funnel on the end. After cranking the engine a few revolutions, it fired right up. There was only a little bit of lifter noise and no banging from the bottom end. I ran the engine this way, varying rpm, for about five minutes. When I noticed only the left choke was opening, I shut it down and swapped the right carbs. At this point, I was basically out of gas, so I put all the tools away and pushed the car back in the garage.
With another hour left before quittin’ time, I figured I’d get back to sanding filler. The problem was the cooler, damp air had left a fine coating of dew on everything. While great for making filler-dust pudding, it wasn’t conducive to cleanly smoothing bodyfiller. Instead, I tackled the gas gage issue. The one that had tested good off the dash, now read ¼ tank once installed. I pulled the two replacements I had left and tested them, this time clipping the gage’s body to ground when plugging it in. I noticed that in both cases, grounding the housing caused a rise in the needle. I did find one that hovered at E with everything hooked up so this one was swapped into the dash, but not before contortions and cutting on sharp sheetmetal. Oh well, the joys of working on cars continues.





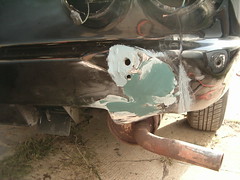
After a walk with the lovely Loriann to buy motor oil at Advance Auto, I filled Ringo’s engine crankcase and added an ounce of ZDDP additive. Then, with my electric drill and a 3/8 diameter bar with a flat milled in one end, I primed the oil system by spinning the pump input at the bottom of the distributor bore for a few seconds noting the Temp/Press light went dark soon after starting. That is a good thing. I also noticed an increase in torque required to turn the pump once the light went off. Also good. I then rotated the engine some and repeated the priming. After going all the way around the engine twice, I pronounced the engine fully primed, pushed it back into the garage, and called it a day.
Yesterday, after lunch, Mikhaila and I took a trip to Sears where I bought a DieHard to replace Ringo’s dead battery.

With another hour left before quittin’ time, I figured I’d get back to sanding filler. The problem was the cooler, damp air had left a fine coating of dew on everything. While great for making filler-dust pudding, it wasn’t conducive to cleanly smoothing bodyfiller. Instead, I tackled the gas gage issue. The one that had tested good off the dash, now read ¼ tank once installed. I pulled the two replacements I had left and tested them, this time clipping the gage’s body to ground when plugging it in. I noticed that in both cases, grounding the housing caused a rise in the needle. I did find one that hovered at E with everything hooked up so this one was swapped into the dash, but not before contortions and cutting on sharp sheetmetal. Oh well, the joys of working on cars continues.
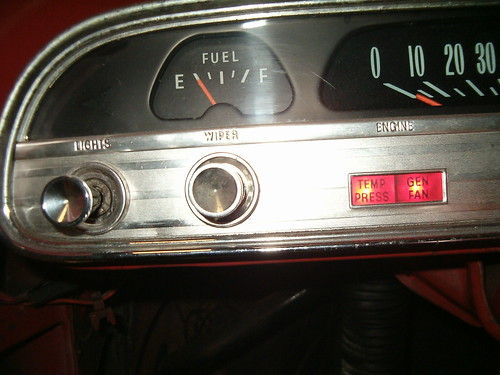
Friday, September 23, 2011
It’s Fun to Make Dust
I got to use one of my favorite tools last night – my inline sander. This thing is a beast for smoothing out bodyfiller. With medium sandpaper on the sander and a mask on my face, I spent a few hours making lots of dust. Towards the end of my evening in the garage, I needed to work on some curved surfaces, so I had to do it by hand. Not nearly as much fun, plus, in the humidity of Baltimore, I was mixing some sweat with the dust. I realized that there are still a number of spots that will need another coat of filler, but that was to be expected.
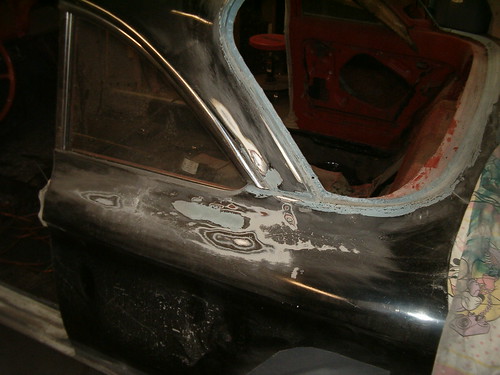
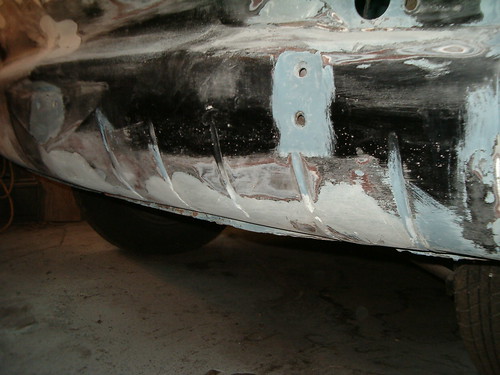

It sure is nice to be making headway.
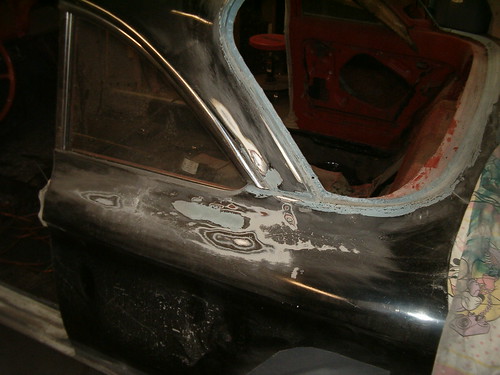
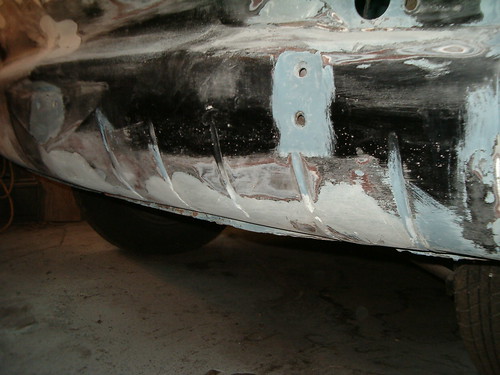

It sure is nice to be making headway.
Thursday, September 22, 2011
Tomorrow I May Make Dust, but Tonight I Bondo
Well, it wasn’t exactly Bondo brand body filler, it was Evercoat, but a facial tissue is still a Kleenex and Evercoat doesn’t work well as a verb. Before mixing up my first batch, though, I had to clear the workbench of carburetor stuff. I re-marked the “good” carb to “acc pump” and put it and an actual good assembly up on the shelf. I also stowed the box of gaskets and the container of extra parts. I didn’t keep count as to how many slighter-larger-than-a-golf-ball batches I made, but by the time I’d filled all the rust holes and paint-less divots, I had just about depleted the contents of the quart can. My eternal optimism causes me to feel confident I won’t need to buy another can, but I’ll only know that once all the sanding is done – and that will start this evening.
There’s no photos today since I am no artist with the spatula.
There’s no photos today since I am no artist with the spatula.
Tuesday, September 20, 2011
And Now For Something Completely Different
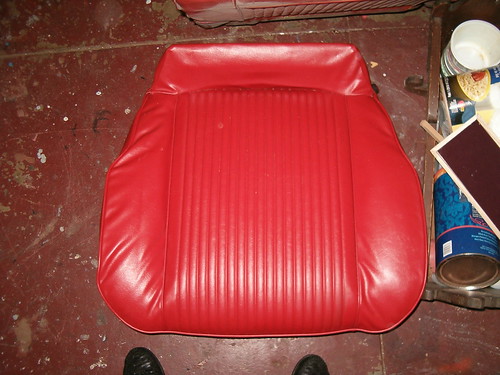
Having had enough of engine and bodywork for a night, I decided to tackle upholstery last evening. I started by carefully disassembling Ringo’s driver seat. Off came the retaining clips,
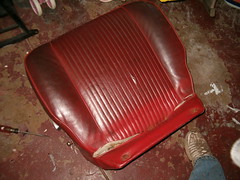
screws, and plastic washers that then allowed me to separate the back from the bottom. Next I removed the two seat tracks and bumpers from the bottom. I took a couple pictures before commencing to cut all the hog rings that held the old cover onto the frame. Since I’ve done this same upholstery job on Heidi’s bucket seats a few years back, I knew what I was in for; and what I was in for would not be fun. Regardless, it wasn’t necessary to closely document the disassembly. With the frame free of vinyl, I dug out the roll of padding material and cut out new pieces for the center and the two bolster. Next I transferred the stiff wires that fit into the sleeves from the old to the new cover. Two wires were damaged, so I found wire that I’d bought for Heidi and cut and formed two new lengths and installed them in their sleeves.
After laying down the new padding over the center portion of the bottom, the first hog rings I installed attached the cover to the rear edge of the center portion. Then I carefully and frustratingly worked my way forward crimping hog rings attaching the side edges of the center portion to the frame wires nestled between the center foam pad and the side bolsters. The success rate for those rings is about 10%, so it took me about an hour to get the dozen rings properly installed.
With those finally in place, the rest of the job went easily. I placed the new padding over the bolsters and pulled the front, side, and back sections into place. Hog rings were crimped all the way around and the two holes for the pins that retain the back were punched. At that point I had used my quota of swear words, so it was time call it a night.

Monday, September 19, 2011
Carburetion Day
Yesterday afternoon was the only opportunity I got to work on the fleet. I made the most of it by first coating all the POR-15 spots with Tie-Coat primer. Once cured, this will provide a good base for bodyfiller or primer.

Since I’ve been playing musical chairs with carburetors – swapping between Lucy and Glinda and rebuilding ones on the shelf – I didn’t know which two of the five carbs I have on the shelf would be the best for Ringo’s rebuilt engine. To alleviate this condition, I used Glinda as my test mule. A while back, I’d swapped one of my racing carburetors onto the driver’s side of the Glinda’s engine to try and fix a problem that ended up not being carb related. That carburetor was still on Glinda, so I pulled it off and marked it good. Next I put on a recently repaired carburetor. This was one that used to be on Lucy, but had a vacuum leak that caused that side of the engine to run lean and overheat. I found that a worn throttle shaft was the cause, so I fixed this by implementing the o-ring/washer/spring repair you can read about here. That carb checked out fine on Glinda, so off it came and on went one that I’d marked with the word “Good”. Well, it wasn’t. By the way, I should note here that my method of testing was removing the main throttle shaft so each carburetor could be operated independently. After running the engine for a few seconds, the bowl in the new carb had filled with gas, and I could blip the throttle linkage on that one or the other carb (or both) and saw how the engine responded. Equal and lag-free response was what I was looking for. With the supposedly good carb, the engine started bogging about twenty seconds after I knew the bowl was full. I shut off the engine and noticed gas running into the venture. Stuck needle. I pulled the top assembly off the carb, checked the needle and seat and found it would hang up due to the little wire linkage that attaches the needle to the float. I removed that piece which I don’t think is really necessary anyway, put the carb back together, started the engine, and everything worked wonderfully. Yes! The next one to go was one that had the word “Rebuilt” on it, and it had the same flooding issue. Off came the top, off came the linkage, back on went the top, and the flooding issue was gone and the engine responded well to throttle blips. Then it was time to put an unknown entity on. This carb had no writing on it. I found the problem with it was a faulty accelerator pump – no little jet of fuel when the throttle is blipped. Since I didn’t have a replacement cup for the pump, I removed this carb for future work and bolted Glinda’s original, repaired carb. After balancing the carburetors and putting the air cleaner assembly back together, I had Victoria take Glinda for a spin around the neighborhood. She came back complaining the idle speed was too high. I hooked up my portable dwellmeter/tachometer and backed down the screws until the speed in Drive was 500 rpm. She drove the car again last night and had no complaints so I guess it’s performing satisfactorily. It will be interesting to see if putting the original ’68 carb will have an impact on the fuel mileage.
A couple issues I discovered and addressed on Glinda while I was using her were a faulty brake light (ended up being a loose socket that I tightened) and broken air cleaner gasket. The latter was a little scary since the engine was trying to suck the part into itself. I didn’t have a replacement, so I just bolted the cleaner assembly back on without a gasket for the time being. It fits quite closely, so it’s a low-risk solution.
With Glinda roadworthy, I installed two of the tested carburetors on Ringo’s engine. One step closer to having his rebuilt engine make its maiden run.


Since I’ve been playing musical chairs with carburetors – swapping between Lucy and Glinda and rebuilding ones on the shelf – I didn’t know which two of the five carbs I have on the shelf would be the best for Ringo’s rebuilt engine. To alleviate this condition, I used Glinda as my test mule. A while back, I’d swapped one of my racing carburetors onto the driver’s side of the Glinda’s engine to try and fix a problem that ended up not being carb related. That carburetor was still on Glinda, so I pulled it off and marked it good. Next I put on a recently repaired carburetor. This was one that used to be on Lucy, but had a vacuum leak that caused that side of the engine to run lean and overheat. I found that a worn throttle shaft was the cause, so I fixed this by implementing the o-ring/washer/spring repair you can read about here. That carb checked out fine on Glinda, so off it came and on went one that I’d marked with the word “Good”. Well, it wasn’t. By the way, I should note here that my method of testing was removing the main throttle shaft so each carburetor could be operated independently. After running the engine for a few seconds, the bowl in the new carb had filled with gas, and I could blip the throttle linkage on that one or the other carb (or both) and saw how the engine responded. Equal and lag-free response was what I was looking for. With the supposedly good carb, the engine started bogging about twenty seconds after I knew the bowl was full. I shut off the engine and noticed gas running into the venture. Stuck needle. I pulled the top assembly off the carb, checked the needle and seat and found it would hang up due to the little wire linkage that attaches the needle to the float. I removed that piece which I don’t think is really necessary anyway, put the carb back together, started the engine, and everything worked wonderfully. Yes! The next one to go was one that had the word “Rebuilt” on it, and it had the same flooding issue. Off came the top, off came the linkage, back on went the top, and the flooding issue was gone and the engine responded well to throttle blips. Then it was time to put an unknown entity on. This carb had no writing on it. I found the problem with it was a faulty accelerator pump – no little jet of fuel when the throttle is blipped. Since I didn’t have a replacement cup for the pump, I removed this carb for future work and bolted Glinda’s original, repaired carb. After balancing the carburetors and putting the air cleaner assembly back together, I had Victoria take Glinda for a spin around the neighborhood. She came back complaining the idle speed was too high. I hooked up my portable dwellmeter/tachometer and backed down the screws until the speed in Drive was 500 rpm. She drove the car again last night and had no complaints so I guess it’s performing satisfactorily. It will be interesting to see if putting the original ’68 carb will have an impact on the fuel mileage.
A couple issues I discovered and addressed on Glinda while I was using her were a faulty brake light (ended up being a loose socket that I tightened) and broken air cleaner gasket. The latter was a little scary since the engine was trying to suck the part into itself. I didn’t have a replacement, so I just bolted the cleaner assembly back on without a gasket for the time being. It fits quite closely, so it’s a low-risk solution.
With Glinda roadworthy, I installed two of the tested carburetors on Ringo’s engine. One step closer to having his rebuilt engine make its maiden run.
Friday, September 16, 2011
Bare Metal Gone
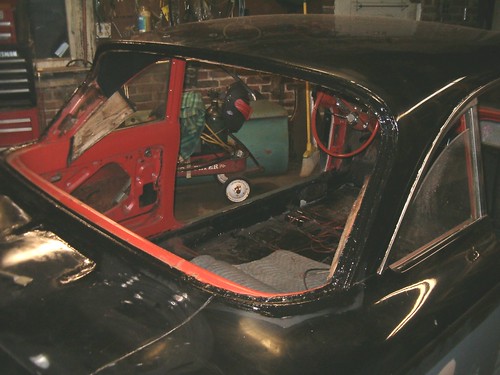
Last night I wanted to blow off fleet maintenance, but the lovely Loriann gently urged me to visit the garage. I’m glad she did because I passed another milestone. The rusted metal is now encapsulated by two coats of POR-15. I did a thorough inspection of Ringo’s exterior to ensure all the rust spots were properly prepped for painting. Then, with gloves donned, I opened my last jelly jar of POR-15 and proceeded to paint the backlight opening, the trunk lid underside and edges, the rusted portions of the front panel and valence, the spot on the engine lid that had blistered from the fire, and assorted other spots on the car. While I waited for the first coat to flash off enough for the second coat, I installed the transmission cable with the recently received o-ring and tightened the parking brake cable. One more coat of POR-15 then went down before I turned out the lights.

Thursday, September 15, 2011
Moving Along
Another evening in the garage and I’m closer to completion. I wire wheeled the window opening to remove residual sealant, bondo, and old paint. It’s down to bare or lightly rusted metal now. I also removed the two fake grill pieces from the panel just aft of the backlight. Underneath those was some rust that also fell prey to the wire wheel. The next step is coating all the exposed metal with two layers of POR-15 and one of Tie-Coat primer and they have to be applied within a specific time frame, so I didn’t have enough evening left to do that task. Instead I cleaned off the trim strips from around the window. I’d like to knock the dents out of these as well, but that is a tedious task I may not choose to devote time to.
Wednesday, September 14, 2011
Ringo Tastes Freedom

With the mulch finally out of the way, I rolled Ringo out of the garage to give him a bath. First, though, I needed to empty and uncover him. Seats came off his roof and carpet and door panels came out of his salon, all to find temporary homes in our basement. Now empty and off jackstands, he rolled easily into the twilight glow. I still can’t believe that it’s been over a year since he was taken off the road. Time flies when you’re having fun.
After a thorough, soapy cleaning of only his exterior, I turned my efforts to sweeping out the garage floor. The lovely Loriann picked that time to come out from the house and ask me why I was cleaning the garage, not the car. “It’s already clean,” I retorted. I should’ve had her help me push the car back in the garage then, but there were still piles of grinding dust in the way.
Once Ringo was back under roof, I decided to tackle the task of adjusting the dragging brake shoes. I’d remembered it being the passenger side, so I jacked that corner up and pulled the wheel. Lo and behold the drum spun freely. Crap! Must’ve misremembered. Back on went the tire, and the jack was used on the opposite corner. Before pulling the wheel, I gave it a spin – no dragging. Pulled the wheel anyway to confirm. Guess the problem fixed itself. I’ll keep an eye on it when I take it out on the road. If it’s still dragging that side will pull when stopping.
With that crossed off the mental to-do list, I decided to tackle the backlight. It hurt to cut the $100 weatherstrip, but it’s really the only safe way to remove the glass. Half an hour later the glass was safely out and sitting on its bottom edge leaning out of the way. This exposed the nastiness of the window channel. For the next hour or so I scraped off the sealant I’d unsuccessfully used to seal the joint. The car was still wet, so this evening, I’ll roll the car back out of the garage and go at the channel with the wire wheel attachment on my grinder. This will prep it for POR-15 and tie-coat primer.


Tuesday, September 13, 2011
Ringo Needs A Bath
Last evening was night of decisions. I decided working with the Evercoat Everglass is not as difficult as I’d envisioned. I decided I’m not automatically going to reinstall the shiny rocker panel trim. I decided the backlight is coming out and the gasket will be replaced. I decided the car will be painted with the backlight out. I decided the front windshield is NOT coming out. I decided not to put the internals into the replacement door until after it is painted. I decided I can’t do any more bodywork until I wash all the grinding dust off the car. Finally, I decided, at 10 PM, to quit for the night.
What circumstances brought me to these conclusions?
First, I mixed and applied three small batches of the new bodyfiller over the welded areas to fill in the pin holes left after grinding. Even though the Everglass is fiber filled, it still spread easily and smoothly.
Second, as I was spreading the filler, I went ahead and filled the screw holes that are used to attach the rocker panel pieces. I’ll let Ariel look at the car before I reinstall these shiny pieces and the stainless trim around the wheel openings. I like the cleaner look, but she may feel differently.
Third, after moving on to locating all the rusted areas that I wanted to properly treat, I took a close look at the backlight. My original plan was to use a better sealant and a special applicator and work with what’s there, but the amount of crap I’ve laid down trying to stop the leaking has made that plan impossible. I started removing the chrome trim from the gasket and that exposed the telltale orange of rust. The backlights gotta’ come out, the opening completely cleaned of sealants, and then the rusted metal will get the POR-15 and Tie-Coat primer treatment before being primed and painted with the rest of the outside of the body.
Fourth, a close inspection of the front windshield gasket as well as a look under the dash indicated the water leaks that are coming in under the dash are very likely not through the windshield gasket, but rather through failed seam sealer under the fresh air intake grill at the base of the windshield.
Fifth, clearing out the rear seat area to give me access to the backlight gasket had me moving the glass and regulator for the replacement door. I thought I’d be smart and get this stuff out of the way by installing it in the door. As I gathered the tools for the task, it occurred to me I’ll be painting the door with the door handle and lock off and it’s harder to reinstall those parts with the window installed. Plus the door is much easier to handle without the extra weight of glass and regulator. So, the door will stay empty as it currently sits.
Sixth, the next project after removing the backlight is cleaning all the surfaces that are to be treated for rust. I didn’t wash Ringo before stating this re-roadification, so there’s a ton of dust and grime that needs to come off before I can lay down any more coatings.
What circumstances brought me to these conclusions?
First, I mixed and applied three small batches of the new bodyfiller over the welded areas to fill in the pin holes left after grinding. Even though the Everglass is fiber filled, it still spread easily and smoothly.
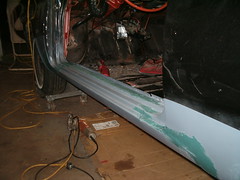
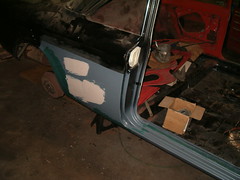
Third, after moving on to locating all the rusted areas that I wanted to properly treat, I took a close look at the backlight. My original plan was to use a better sealant and a special applicator and work with what’s there, but the amount of crap I’ve laid down trying to stop the leaking has made that plan impossible. I started removing the chrome trim from the gasket and that exposed the telltale orange of rust. The backlights gotta’ come out, the opening completely cleaned of sealants, and then the rusted metal will get the POR-15 and Tie-Coat primer treatment before being primed and painted with the rest of the outside of the body.
Fourth, a close inspection of the front windshield gasket as well as a look under the dash indicated the water leaks that are coming in under the dash are very likely not through the windshield gasket, but rather through failed seam sealer under the fresh air intake grill at the base of the windshield.
Fifth, clearing out the rear seat area to give me access to the backlight gasket had me moving the glass and regulator for the replacement door. I thought I’d be smart and get this stuff out of the way by installing it in the door. As I gathered the tools for the task, it occurred to me I’ll be painting the door with the door handle and lock off and it’s harder to reinstall those parts with the window installed. Plus the door is much easier to handle without the extra weight of glass and regulator. So, the door will stay empty as it currently sits.
Sixth, the next project after removing the backlight is cleaning all the surfaces that are to be treated for rust. I didn’t wash Ringo before stating this re-roadification, so there’s a ton of dust and grime that needs to come off before I can lay down any more coatings.
Monday, September 12, 2011
Moving Right Along
This weekend was filled with a hodge-podge of activities; many were typical chores of a homeowner seemingly unrelated to fleet maintenance (pushing grout into the cracks of bathroom tile floor, putting away window A/C units, pruning rose bushes, spreading mulch and making a long-overdue run to the dump). The last two actually were important towards getting Ringo back on the road. We’ve had a pile of mulch in our driveway for the last couple months. Since it blocks both the garage door and the gate to the backyard, it had to be moved before I could empty the utility trailer now overflowing with junk Corvair parts and yard cuttings. The lovely Loriann and I shoveled, wheelbarrowed, and spread mulch until we’d blazed a pathway wide enough to maneuver the trailer out of the yard. This same pathway is also wide enough to squeeze Ringo through for his maiden journey which will, I hope, be in the very near future.
After returning from the dump, I took my dirty self out to the garage and removed Ringo’s gage cluster from the dashboard.
After disassembly, I cleaned the speedometer drive and lubricated it with WD40 until it spun freely again. I replaced the gas gage, cleaned the clear piece plastic lens, and reassembly the cluster. Installing it back into the dash wasn’t too bad until it came to the part where I got to lie on my back and plug all the little bulb sockets back into their mounting holes. With that complete, I lubricated the steering shaft bearing as best I could, and then reinstalled the steering wheel and all its hardware.
Next on the agenda was ensuring the heating system worked. Previously, Ariel couldn’t run Ringo’s heater fan since it would blow the fuse. I cleaned all the connections to the fan motor, so now was the time to test it. With the battery charger providing juice through the basically dead battery, I turned the switch to high and was greeted with a nice flow of air out the two floor ducts. I left the motor running while I took a short break and came back to the garage a half-hour later and found the motor still running nicely. Hopefully, it behaves the same way when powered by the alternator. While testing the motor, I discovered the cable that actuates the right defroster vent was broken. I disassembled it from the lever and the vent door, and added it to my to-buy list.
I also laid out the two carpet pieces and gave them a good cleaning. Sadly, the water that has leaked into Ringo’s interior for the last few years has taken its toll. The carpet is not the nice red it was when new, but rather a spotty, orange-ish not pleasing to the eye. After talking with Jeff at the Corvair Ranch this morning, I intend to try spray vinyl dye to resurrect these pieces since I can’t afford new ones.
Today the lovely Loriann is buying a quart can of Evercoat Everglass body filler. I chose this filler since it is supposed to be waterproof and I need to fill the small holes and rusted through areas of Ringo’s body. I won’t be able to paint the backside of the filler, so it’s important it doesn’t absorb any moisture that would cause the new paint to bubble. While a quart is probably not enough to complete the job, it will be enough for a first coat – the one that plugs the holes.
After returning from the dump, I took my dirty self out to the garage and removed Ringo’s gage cluster from the dashboard.
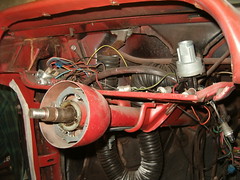
Next on the agenda was ensuring the heating system worked. Previously, Ariel couldn’t run Ringo’s heater fan since it would blow the fuse. I cleaned all the connections to the fan motor, so now was the time to test it. With the battery charger providing juice through the basically dead battery, I turned the switch to high and was greeted with a nice flow of air out the two floor ducts. I left the motor running while I took a short break and came back to the garage a half-hour later and found the motor still running nicely. Hopefully, it behaves the same way when powered by the alternator. While testing the motor, I discovered the cable that actuates the right defroster vent was broken. I disassembled it from the lever and the vent door, and added it to my to-buy list.
I also laid out the two carpet pieces and gave them a good cleaning. Sadly, the water that has leaked into Ringo’s interior for the last few years has taken its toll. The carpet is not the nice red it was when new, but rather a spotty, orange-ish not pleasing to the eye. After talking with Jeff at the Corvair Ranch this morning, I intend to try spray vinyl dye to resurrect these pieces since I can’t afford new ones.
Today the lovely Loriann is buying a quart can of Evercoat Everglass body filler. I chose this filler since it is supposed to be waterproof and I need to fill the small holes and rusted through areas of Ringo’s body. I won’t be able to paint the backside of the filler, so it’s important it doesn’t absorb any moisture that would cause the new paint to bubble. While a quart is probably not enough to complete the job, it will be enough for a first coat – the one that plugs the holes.
Thursday, September 8, 2011
My Unshakeable Optimism and The List Revisited
Last night I wanted to refresh my memory as to what issues initially caused Ringo’s re-roadification, so I referred back to my blog post that showed the to-do list only to find (with much sadness and frustration) that it was dated more than one year ago. It seems that all of my missed self-imposed deadlines never diminish my optimism. I always believe a project will take far less time than it inevitably does. I carry on a regular e-mail conversation with my close car buddy, Bill, and my outbox has more than a dozen sent messages where I write about stating the roadification of my LeMans. All of these have me starting “in the next couple months”. Why has this Ringo project taken me so long? And I have to be honest with myself – while there’s a visible light at the end of the tunnel, there’s no definitive timetable for his road-readiness.
Oh well, life goes on. We all have the vehicles we need to meet our daily commitments, so I need not get so negative.
But I digress; back to the list. I wanted to refer to it because I’m at a point where I want to take care of the non-bodywork stuff while I wait for the funds to purchase the epoxy bodyfiller required to continue Ringo’s exterior repairs. Here are the items I dealt with last night but not before finishing the muffler installation:
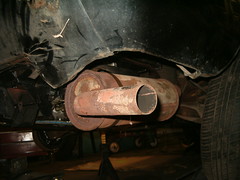
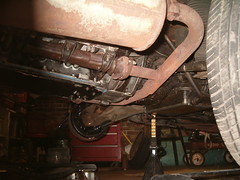
Floor
While I’d previously welded down all the patch edges inside the car, there were some underside edges that were flapping in the breeze so to speak. After maing sure I still had some welding gas in the tank, I exposed bare metal in the spots to be welded, donned all my welding garb, and rolled the jack under the car. I used the jack to hold the loose edges snug against the mating panel while laying down sufficient beads to do the job. While lying under the car, I noticed a number of areas that need a couple coats of POR-15. On the bright side, there is metal there to coat.
Tighten Steering
I removed the steering wheel and tried to carefully remove the bearing assembly so I could clean it and put in new grease. I didn’t get much farther than inspection since I was unable to move the bearing on the steering shaft. I submitted a message on the CorvairCenter forum asking for guidance on how to proceed. We’ll see if anyone responds.
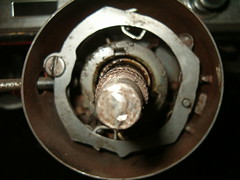
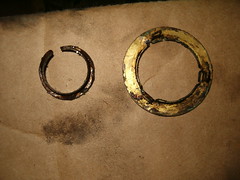
Tighten Brakes
While this item was intended to remind me to tighten the parking brake cable, I also used it as the reminder to complete the rebuild of the rear brakes. I dug out my one-person brake bleeder kit and bled the air out of the two rear brake cylinders. I still need to do some work on the right side shoes to ensure there’s the proper clearance to the drum. While that will require disassembly of that side, it won’t affect the wheel cylinder.
Gas Gauge
This task was to make sure the gauge behaved properly – F mark when full and E mark when empty. Before entering re-roadification the needle wouldn’t drop much below ½ tank regardless of how empty the tank was. Research indicated the resistance when the sender is bottomed (empty tank) should be zero, so I made sure the tank was empty by pumping out the last gallon left in the tank (nice to have fresh gas for the fresh engine anyway) and hooked up my voltmeter. While the reading wasn’t zero, it was in the millivolts. Next, I went to the shelf and found four gauges I’d pulled from previous dashes to test. The first one I tried showed far below E before plugging in and didn’t move once it was connected. Trash. The second one read about ½ tank before and just below E after being plugged in. I’ll go with that one. Now I just need to pull the dash and install it. That’ll give me good access to the speedometer so I can address another item on the list.
Oh well, life goes on. We all have the vehicles we need to meet our daily commitments, so I need not get so negative.
But I digress; back to the list. I wanted to refer to it because I’m at a point where I want to take care of the non-bodywork stuff while I wait for the funds to purchase the epoxy bodyfiller required to continue Ringo’s exterior repairs. Here are the items I dealt with last night but not before finishing the muffler installation:
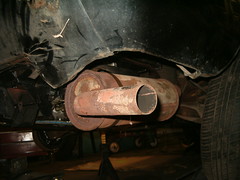
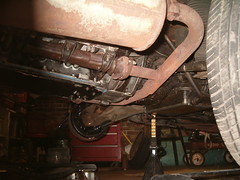
Floor
While I’d previously welded down all the patch edges inside the car, there were some underside edges that were flapping in the breeze so to speak. After maing sure I still had some welding gas in the tank, I exposed bare metal in the spots to be welded, donned all my welding garb, and rolled the jack under the car. I used the jack to hold the loose edges snug against the mating panel while laying down sufficient beads to do the job. While lying under the car, I noticed a number of areas that need a couple coats of POR-15. On the bright side, there is metal there to coat.
Tighten Steering
I removed the steering wheel and tried to carefully remove the bearing assembly so I could clean it and put in new grease. I didn’t get much farther than inspection since I was unable to move the bearing on the steering shaft. I submitted a message on the CorvairCenter forum asking for guidance on how to proceed. We’ll see if anyone responds.
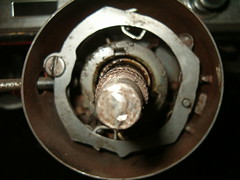
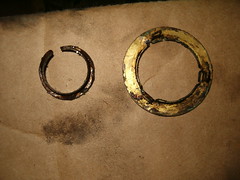
Tighten Brakes
While this item was intended to remind me to tighten the parking brake cable, I also used it as the reminder to complete the rebuild of the rear brakes. I dug out my one-person brake bleeder kit and bled the air out of the two rear brake cylinders. I still need to do some work on the right side shoes to ensure there’s the proper clearance to the drum. While that will require disassembly of that side, it won’t affect the wheel cylinder.
Gas Gauge
This task was to make sure the gauge behaved properly – F mark when full and E mark when empty. Before entering re-roadification the needle wouldn’t drop much below ½ tank regardless of how empty the tank was. Research indicated the resistance when the sender is bottomed (empty tank) should be zero, so I made sure the tank was empty by pumping out the last gallon left in the tank (nice to have fresh gas for the fresh engine anyway) and hooked up my voltmeter. While the reading wasn’t zero, it was in the millivolts. Next, I went to the shelf and found four gauges I’d pulled from previous dashes to test. The first one I tried showed far below E before plugging in and didn’t move once it was connected. Trash. The second one read about ½ tank before and just below E after being plugged in. I’ll go with that one. Now I just need to pull the dash and install it. That’ll give me good access to the speedometer so I can address another item on the list.
Wednesday, September 7, 2011
More Engine Readying
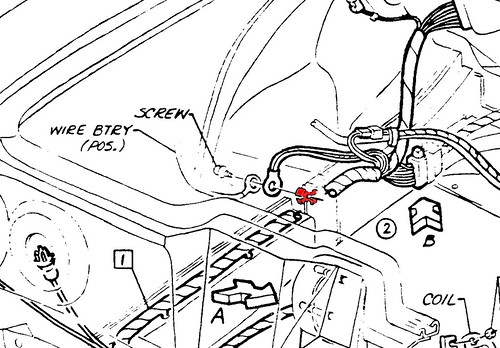
Last night the focus was electrical and exhaust. As I mentioned in a recent post, I want to keep Ringo’s original charging wiring intact in case I need to revert. That includes all the little spade terminals. The LM alternator-based wiring is rather straightforward. With the voltage regulator 4-wire connector as a hub, there’s a striped wire going to the dashlight, a pair of wires going to the Field/Armature connector at the alternator and a red wire connecting to the main 12 V leads at the junction (also know as the horrid little plastic thingy).
A little on that horrid little plastic thingy. It’s been a source of frustration for many LM owners. This small, red terminal resides in the engine compartment near the battery and its sole function is to provide a means to connect the positive wire that comes from the alternator to the smaller wire from the battery. Over time the plastic can break down and eventually fail causing either a massive short to the car body or an open circuit with a resulting dead battery and/or loss of current to the car’s electrical components. Either way, a bad thing. Now in their defense, the designers did need an easy and robust method of connecting high-current wires to each other, and this part probably worked flawlessly for the typical ten-year life of the car (yes, we’re talking the 60s here).
Back to last night’s activities. The existing EM wire harness has functionality of the junction built in at the B terminal of the voltage regulator. Since this terminal does not exist in the LM regulator, I used a screw, washer, and nut to connect a new red wire to the existing battery wire and the main wire that provides 12 volts to the entire car. The other end of this new red wire mated to the output wire from the alternator at the LM junction. I used the same screw-washer-nut scheme to connect the sensing wire from the LM harness to the existing sensing wire that goes to the dash idiot light. Finally, I carefully wrapped all the exposed conducting metal with a few layers of electrical tape and constrained all the wires with zip-ties. If all goes well, I will clean this assembly up by removing the ugly interfaces and soldering the wires together with shrink tubing for insulation. Will I keep the horrid little plastic thingy? I haven’t decided.
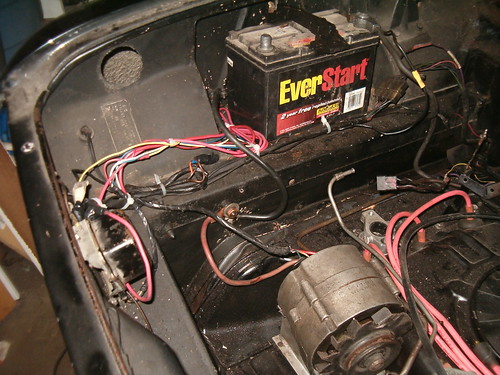
With the electrical in place including connecting the positive lead to the coil, I turned my attention to the exhaust. Of course, this too, could not be straightforward. EMs use a cylindrical muffler, while LMs used one with an oval cross-section. The exhaust pipe that Ringo had prior to teardown had a failed flange, but a usable round muffler. I have a GUP exhaust pipe with a LM muffler on the shelf (actually on the floor). However, the new mounting strap I got from the Corvair Ranch is for the round style so it’s too short to use with oval style. That meant I got to remove mufflers from exhaust pipes – NOT fun. Having fought this fight a few times in the past, I know the futility of trying to do this neatly. The only success I’ve had is grinding two longitudinal slices through the outer (muffler) pipe only up to the point where the clamp had been and then peeling back the outer muffler pipe until the inner exhaust pipe is free. I did this on the oval setup so I didn’t damage the exhaust pipe. Since the exhaust pipe on the round assembly was going to the recycler anyway, I just cut off the exhaust pipe outboard of the union, and wedged the inner pipe loose with a small chisel (read screwdriver) and a hammer. With the muffler loose, I wasn’t home free since the clamp had put a not-so-nice impression in the muffler pipe that precluded easily inserting the replacement exhaust pipe. Using my big channel-lock pliers and a small round bar, I pressed out enough of the impression that some banging satisfactorily brought pipe and muffler together.
Bolting the pipe/muffler assembly into place is not too big a deal, and I got the flanges secured without issue. Since it was nearing 11, adjusting and tightening the hanger will wait until tonight.
Thursday, September 1, 2011
The Rest of the Fleet Gets Some Press
Since Ringo’s been sucking up most of the fleet time, he’s also been the subject of most of the blog posts. I’ll use today’s missive to catch up on the rest of the fleet.
Lucy has been behaving quite nicely for the past few months returning 20+ mpg and demanding only a tiny bit of my precious time since I had my “Most Frustrating Evening.” The incident was a failure of the turn signal switch. The problem was the sliding contact assembly wouldn’t slide. After making sure both brake lights worked, I drove around with the inability to let drivers around me know of my turning and lane changing intentions. Last Sunday, I spent an hour or so removing, diagnosing, and subsequently swapping the broken assembly for a GUP off the shelf. During the diagnosis phase, I discovered that one of the contacts was loose and was poking into the cavity where the slider was to slide. Into the trash the nearly 50-year-old went. Ariel now has Lucy up in Millersville leaving me with the Surburban as my daily-driver.
Glinda has also been behaving giving Victoria nearly 18 miles per gallon of expensive 93 octane gasoline. I do, however, need to reward her by scheduling some time to tighten the fasteners retaining her driver’s door handle. I also promised Victoria we’d try out my new buffer on scuffs that adorn a few places of Glinda’s Artesian Turquoise.
Finally there’s Heidi. I had a nice conversation with Brianna yesterday covering a number of topics. The one pertinent to this blog is that, even though she hasn’t driven Heidi, she’s not ready to part with her. Heidi has been sitting for most of the last year after a couple incidents of stranding Brianna foremost of which was detailed by my post, of August 16. She’s unwilling to risk another stranding until I’ve given the car a thorough shakedown. The lovely Loriann and I will be visiting Brianna and Nich next month, so we’ll be taking the Suburban and the tow bar and Heidi will come and live with us in Baltimore until next Spring.
Lucy has been behaving quite nicely for the past few months returning 20+ mpg and demanding only a tiny bit of my precious time since I had my “Most Frustrating Evening.” The incident was a failure of the turn signal switch. The problem was the sliding contact assembly wouldn’t slide. After making sure both brake lights worked, I drove around with the inability to let drivers around me know of my turning and lane changing intentions. Last Sunday, I spent an hour or so removing, diagnosing, and subsequently swapping the broken assembly for a GUP off the shelf. During the diagnosis phase, I discovered that one of the contacts was loose and was poking into the cavity where the slider was to slide. Into the trash the nearly 50-year-old went. Ariel now has Lucy up in Millersville leaving me with the Surburban as my daily-driver.
Glinda has also been behaving giving Victoria nearly 18 miles per gallon of expensive 93 octane gasoline. I do, however, need to reward her by scheduling some time to tighten the fasteners retaining her driver’s door handle. I also promised Victoria we’d try out my new buffer on scuffs that adorn a few places of Glinda’s Artesian Turquoise.
Finally there’s Heidi. I had a nice conversation with Brianna yesterday covering a number of topics. The one pertinent to this blog is that, even though she hasn’t driven Heidi, she’s not ready to part with her. Heidi has been sitting for most of the last year after a couple incidents of stranding Brianna foremost of which was detailed by my post, of August 16. She’s unwilling to risk another stranding until I’ve given the car a thorough shakedown. The lovely Loriann and I will be visiting Brianna and Nich next month, so we’ll be taking the Suburban and the tow bar and Heidi will come and live with us in Baltimore until next Spring.
Subscribe to:
Posts (Atom)