Sunday afternoon was the weekend’s car-time. I started out addressing some small issues on Glinda. The right backup light socket has fallen out of its housing a few times since putting her back on the road. I bent the two metal tangs and popped the socket back into place. Everything’s nice and snug now. One evening last week, I watched Victoria drive away and noticed that Glinda’s right taillight was out. Thinking the bulb had a burnt element, I removed it from its socket and tested it – all was good. After cleaning the contacts and applying some bulb grease, I twisted it into place – still out and the bulb was a little loose feeling. The socket is a multi-piece affair -a metal shell inside the plastic housing with the spring contacts in the bottom of the housing. If the shell is not bottomed out in the housing, the contacts don’t touch. So pushing the shell down resulted in a reliable connection. Checking the oil level indicated it was on the add mark, so a quart of 30 wgt. Rotella went into the crankcase. On to interior issues. At my last trip to the FLAPS, I had purchased a couple bulbs to replace a burned out courtesy light and the dead one that illuminated the heater controls, so I installed them in their sockets and snapped the sockets into place. Finally, in response to Victoria noticing the right speaker didn’t seem to be as loud as the left one, I made an adjustment to the crossover control her speaker set has. Sounds more even now, but I asked her to confirm during her next drive.
With Glinda squared away, I headed into the garage to turn my attention to Ringo’s re-roadification. Even though it appears I’ll be trading Betty for a running engine, I need to be ready with a backup in case bad compression breaks the deal. When disassembling the 95 HP engine (the best candidate for my back-up plan) out of the Old Betty, I had to grind off some of the head nuts. I was able to remove the all but one damaged stud. The stubborn one had resisted all attempts including vise gripping and repeated attempts with the rounded nut socket.
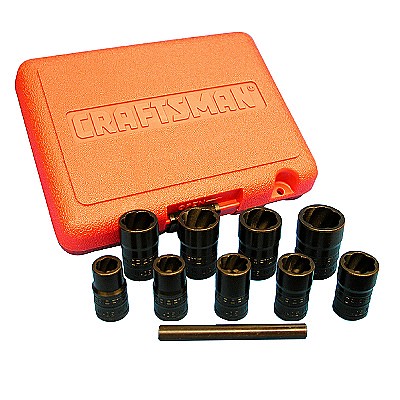
Each attempt with the latter resulted in the stud shearing off at the face of the socket. After the last attempt, the stud was only protruding about a quarter of an inch. I had read about welding a nut to the stud and how the heat seemed to break things loose, so I rolled my wagon-full of MIG welder over to the engine stand. After thoroughly cleaning both the stud end and a decent nut, I dropped the nut over the stud, cranked up the voltage on the welder from its sheetmetal setting and welded the two together. Sadly, the weld would not penetrate the stud enough to get a good bond. Looks like I’ll be drilling this one out.
Knowing I’ll be making lots of metal dust in the next few weeks, I put garbage bags over the 95 HP engine block assembly and the block that came out of Ringo. The last trip to the FLAPS also yielded a loaner valve spring compressor, so I decided to begin the tear down of the 95 HP heads. Even if I don’t end up using this engine, having these heads cleaned up and ready to install will be a good idea. By the time I had the workbench cleared off and the exhaust manifolds removed, it was time to knock off for dinner.
This morning I placed an order with Clark’s for set of ignition points and a distributor gasket for Glinda and for Ringo I ordered two carburetor rebuild kits, a quart of POR-15, and a set of valve stem seals. Last week I ordered replacement rear floor pieces from Rock Auto. I wanted to support Clark’s and buy there perfect reproductions, but I couldn’t justify the additional $100. Since Ringo is far from a show car, inexact floorpans are not a problem.
No comments:
Post a Comment